
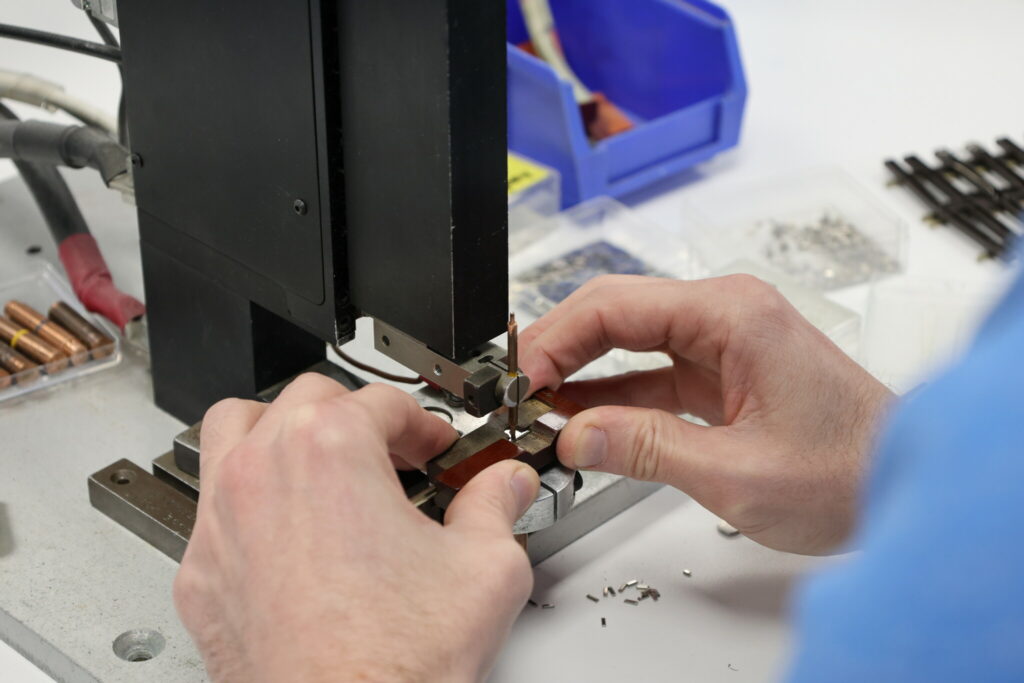
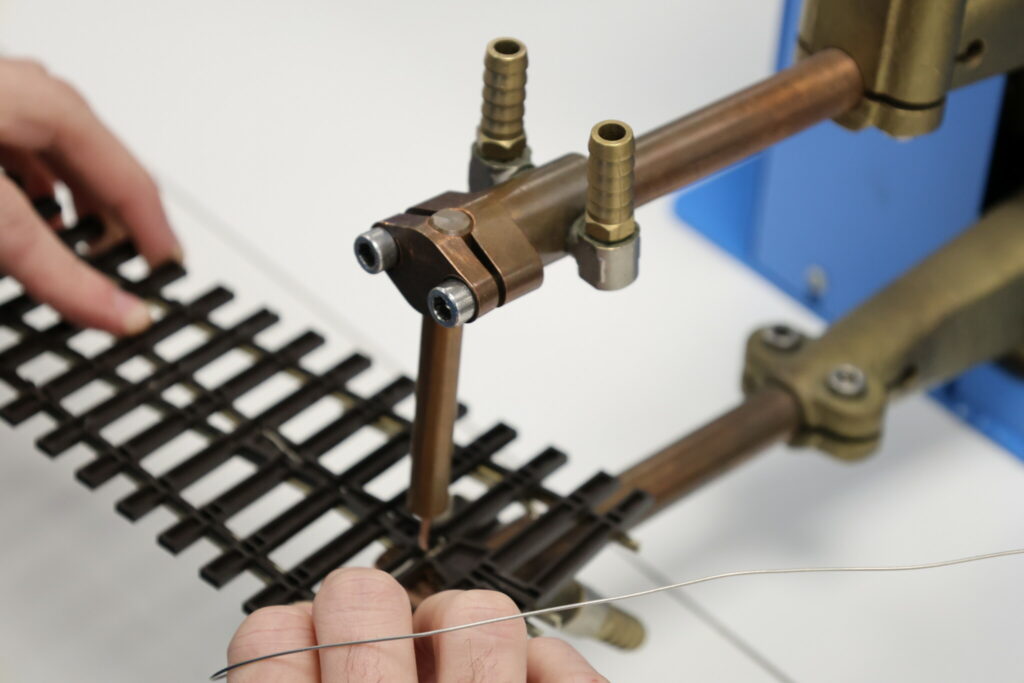
The Turnout Assembly process is a crucial stage in the production of railway turnouts, ensuring precision, quality, and adherence to specific standards. The assembly involves several meticulous steps to guarantee that each turnout meets the highest industry standards.
The process begins on the point assembly production line, where a team of experienced operatives is dedicated to fitting the point blade assembly. The expertise of these operatives is paramount in ensuring the proper alignment and functionality of the turnout. The point blade assembly is a critical component that allows the railway switch to guide trains onto different tracks.
Following the assembly, the turnout undergoes a rigorous inspection process. This involves both electrical testing using a specialized test box and operational testing with a locomotive. The electrical tests verify the conductivity and integrity of the components, while the operational tests ensure smooth and reliable movement of the turnout point blades when subjected to the forces exerted by a locomotive. Visual checks are also conducted to assess the overall quality and appearance of the turnout.
Once the turnout passes the inspection, it moves to the point packing department. Here, the turnout is carefully packed into a clear sleeve along with a descriptive insert card that provides information about the specific type of turnout. This meticulous packaging not only protects the product during transit but also facilitates easy identification for customers.
It’s worth noting that the company offers an extensive range of turnouts, catering to different track specifications and customer requirements. This includes turnouts with designations such as C100, C83, C75, C70, C80, and the specialized C55 for specific customer needs. Additionally, the company introduces innovation with the TT range, showcasing a commitment to staying at the forefront of industry developments.
The mention of the C75B/H turnout, which was the standard on the entire British railway network until the introduction of flat bottom rails around 1960, reflects the company’s historical significance and adaptability to evolving industry standards.
Within the Turnout Assembly department, the company utilizes a semi-automatic point blade curving tool to curve the point blades. This additional step ensures that the point blades are precisely shaped to fit the specific curvature requirements of the turnouts, contributing to the overall efficiency and reliability of the railway infrastructure.
Once the entire process is completed, the finished turnouts and associated track components are sent to the finished goods store for distribution. This marks the culmination of a meticulous production process, highlighting the company’s dedication to delivering high-quality railway turnouts to its customers.
The meticulous process of crafting our large-scale turnouts begins with a dedicated team of highly experienced individuals who bring their expertise to every stage of assembly. The intricate work starts with the insertion of rails into the plastic mouldings, meticulously aligned on our expansive points bench. Each point blade is then carefully fitted to ensure seamless functionality.
A critical aspect of our assembly process involves wire welding, a technique employed to secure the components in place with precision. Utilizing our advanced spot welders, the turnout undergoes pelleting, ensuring a robust and durable connection between the various parts. This attention to detail in the welding process guarantees the longevity and reliability of our turnouts.
Following the assembly and welding stages, our skilled team undertakes a comprehensive quality check. This evaluation involves both visual inspection and electrical testing using a specialized test box. The team meticulously examines every detail, ensuring that each turnout meets the highest standards of craftsmanship and functionality.
To further guarantee the performance of our turnouts, a locomotive is run up and down the completed assembly several times. This dynamic testing process ensures that the turnout functions seamlessly under real-world conditions, meeting the stringent requirements of our quality assurance protocols.
Once the assembly, welding, and testing phases are successfully completed, the turnout is ready for packaging. The carefully crafted turnout is packed securely and then dispatched to our finished goods store, where it awaits distribution. Our commitment to precision, quality, and thorough testing ensures that each turnout leaving our facility meets the exacting standards expected by our customers.
The operations within this department are intricately designed to ensure the production of high-quality wagons that meet both aesthetic and functional standards. The process begins with our skilled spray operatives, who meticulously apply coatings to the wagons using spray guns within our dedicated spray booth. This step not only enhances the appearance of the wagons but also serves as a protective layer.
Once sprayed, the wagons undergo a crucial drying period, allowing the applied coatings to set and adhere properly. This meticulous drying phase ensures the longevity of the coatings and contributes to the overall durability of the wagons.
Following the drying process, the wagons move to the print team, where intricate designs come to life. Utilizing advanced ink jet printers, our print team applies a diverse range of prints to the wagons. The prints vary widely, ranging from simple two-letter white prints with small text to more elaborate designs featuring multiple colours. The versatility in prints adds a unique touch to each wagon, catering to diverse preferences and requirements.
All the wagon liveries, which serve as the foundation for the prints, are carefully sourced by our innovations team. This team not only selects visually appealing designs but also collaborates in the creation of custom artwork required for production. Their involvement ensures that the wagons not only meet quality standards but also align with the latest trends and market demands.
Once the printing process is successfully completed, the wagons move to the assembly phase. Here, they are meticulously put together, and a crucial quality control step is taken. The assembled wagons are then placed on a piece of track for a thorough wheel test, ensuring that the wheels run freely and smoothly. This meticulous testing phase guarantees that the final product meets not only aesthetic expectations but also functional requirements.
After passing the quality control and testing stages, the wagons undergo a final visual inspection to ensure that they meet the highest standards of quality. Any imperfections or deviations are promptly addressed, ensuring that only flawless products move forward.
Finally, the completed and approved wagons are carefully packed and sent to our finished goods store. From there, they are distributed to various destinations, meeting the demands of our customers. The detailed and comprehensive process within this department showcases our commitment to delivering wagons that not only showcase artistic designs but also uphold the highest standards of quality and functionality.
Our dedicated team in this department takes pride in meticulously packing all the essential accessories required to bring your model layout to life. We understand that every layout is unique, and we strive to provide a comprehensive range of items to cater to diverse preferences.
One of our specialties lies in offering a diverse selection of switches and switch housing units. These components play a crucial role in operating your layout efficiently, allowing you to customize the control and movement of your model trains. Whether you’re a seasoned enthusiast or just starting, our assortment caters to various scales and preferences.
For those enthusiasts who appreciate the art of detailing, we take great care in packing PECO kits and accessories. These intricately designed components add a touch of realism and aesthetic appeal to your layout. From miniature buildings to finely crafted figurines, our PECO kits ensure that every aspect of your model world is thoughtfully considered.
Additionally, our team is proud to assemble and pack our highly sought-after starter set unit trackage system. Available in 00, N, and 009 rail codes, these starter sets provide a convenient and accessible entry point for model railway enthusiasts. The trackage system is designed to be user-friendly, making it ideal for both beginners and experienced hobbyists looking to expand their layouts.
We understand that the success of your model railway project depends on the quality and variety of accessories available. That’s why our team goes above and beyond to curate a selection that caters to the diverse needs and preferences of our customers. From the foundational elements like switches and trackage to the finer details of scenery and structures, we ensure that every item packed meets our high standards of quality and authenticity.
At our core, we are not just providing accessories; we are contributing to the joy and satisfaction of creating a unique miniature world. As you unpack our carefully curated products, we hope you feel the passion and dedication that went into assembling each item, bringing your model railway vision one step closer to reality.
In our odds/miscellaneous bench, we play a crucial role in ensuring the seamless operation of your model railway layout. One of our primary responsibilities is managing the switches in the PECO Lectrics range, which serve as the nerve centre of your layout’s power distribution. These switches enable you to control various aspects of your model railway, from changing the direction of trains to activating different sections of the track.
The PECO Lectrics range of switches is known for its reliability and precision, allowing you to have precise control over your layout. Whether you’re a model railway enthusiast or a serious hobbyist, the switches on our odds/miscellaneous bench are designed to meet the demands of your intricate railway system.
In addition to managing switches, we house our 00 & NG joiner fitting machines on this bench. These specialized machines play a crucial role in the construction and maintenance of your railway track. The 00 joiner fitting machine is tailored for standard gauge tracks, while the NG joiner fitting machine is designed for narrow gauge applications.
These fitting machines serve a unique purpose — they stamp the joiner to the rail, ensuring a secure and reliable connection. The precision of this process is paramount for the smooth running of your trains. By creating a perfect join between the rails, these machines contribute to the overall stability of the track, minimizing disruptions and optimizing the performance of your model trains.
Our commitment to excellence extends beyond just providing tools; it encompasses the assurance that your model railway layout operates flawlessly. Whether you’re a novice or an experienced model railway enthusiast, the odds/miscellaneous bench is where the intricacies of technology and craftsmanship come together to enhance the functionality and aesthetics of your model railway experience.
So, as you navigate the world of model railways, rest assured that the odds/miscellaneous bench is working diligently behind the scenes, ensuring that your layout not only meets but exceeds your expectations in terms of precision, reliability, and overall enjoyment.
The efficiency and precision of our welding process play a pivotal role in the successful fabrication of turnouts and crossings at our facility. Our dedicated team of skilled welders utilizes state-of-the-art spot welders to ensure the meticulous placement of welding wire in the assembly of turnouts across various specifications.
Our scope of work extends from the robust C100/75 & 75B/H/83/70 turnouts to the more compact C80/55 models, encompassing the entire spectrum of railway infrastructure requirements. Furthermore, we pride ourselves on staying at the forefront of innovation with the inclusion of our newly developed TT range, which represents the latest advancements in turnout technology.
Each turnout we produce is characterized by a distinct welding style, ranging from insulfrogs to electro frogs, and including our innovative Unifrog turnouts. This diversity in welding techniques underscores our commitment to tailoring our approach to meet the specific demands of each turnout design, ensuring that the final product meets the highest standards of quality and functionality.
The synergy between our welding team and point assembly team is a critical component of our production process. Both departments operate in tandem, necessitating constant communication and collaboration. This close-knit teamwork is essential as the welding team must provide the necessary components and specifications to the point assembly team, and vice versa. This seamless exchange of information ensures that each department is well-informed about the unique requirements of the turnouts, leading to a cohesive and streamlined production workflow.
Our commitment to precision, innovation, and effective communication within our teams is what sets us apart in the industry. By fostering a culture of collaboration and continuous improvement, we not only meet but exceed the expectations of our clients, delivering turnouts that stand at the intersection of reliability and cutting-edge technology.